استابلایزر حرارتی
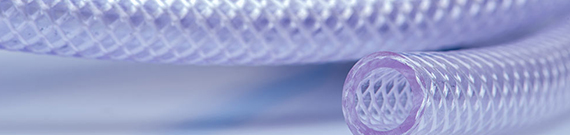
پلیوینیل کلراید (PVC) یکی از پرکاربردترین پلیمرهای صنعتی در دنیا محسوب میشود که به دلیل ویژگیهایی همچون مقاومت شیمیایی، انعطافپذیری در فرمولاسیون، خواص مکانیکی مطلوب و هزینه تولید مناسب، جایگاه ویژهای در صنایع مختلف پیدا کرده است. با این حال، یکی از چالشهای اصلی در استفاده گسترده از این پلیمر، ضعف ذاتی آن در برابر حرارت است. ساختار مولکولی PVC به گونهای است که در مواجهه با دماهای بالا و تنشهای مکانیکی ناشی از فرایندهای شکلدهی، دچار تخریب حرارتی میشود. در این نقطه، استابلایزر حرارتی یا پایدارکننده حرارتی نقش حیاتی خود را ایفا میکند.
ساختار شیمیایی PVC و دلایل ناپایداری حرارتی
PVC یک پلیمر کلردار است که در ساختار زنجیرههای پلیمری آن، پیوندهای کربن-کلر وجود دارد. این پیوندها در برابر حرارت ناپایدارند و با افزایش دما، دچار گسست میشوند. فرآیند تخریب PVC با آزاد شدن گاز HCl (هیدروژن کلرید) آغاز شده و این پدیده منجر به واکنشهای زنجیرهای هیدروکلرزدایی و اکسایشی میگردد که نتیجه آن تغییر رنگ، کاهش خواص مکانیکی، شکنندگی و در نهایت افت شدید کیفیت محصول نهایی است. این تخریب نهتنها در مراحل تولید بلکه در طول عمر محصول نیز میتواند رخ دهد، بهویژه در مواجهه با تابش فرابنفش (UV) یا دمای بالا در محیط کاربری.
نقش استابلایزر حرارتی در حفظ پایداری PVC
استابلایزر حرارتی ترکیبی از مواد شیمیایی است که با جذب یا خنثیسازی HCl آزادشده، جلوگیری از واکنشهای زنجیرهای و پایدارسازی رادیکالهای آزاد، مانع از ادامه تخریب PVC میشود. این مواد در فرآیندهای شکلدهی مانند اکستروژن، تزریق، کلندرینگ و کامپاندینگ استفاده شده و موجب میشوند تا پلیمر در برابر دما و شرایط مکانیکی مقاومتر عمل کند. در کنار آن، استفاده از استابلایزر حرارتی موجب بهبود فرآیندپذیری، افزایش شفافیت، جلوگیری از زردشدگی، بهبود خواص سطحی و ارتقاء خواص نهایی محصول میگردد.
دستهبندی استابلایزرهای حرارتی PVC
استابلایزرهای حرارتی بر اساس ترکیب شیمیایی و نوع عملکرد به گروههای مختلفی تقسیم میشوند که انتخاب نوع مناسب آن بسته به کاربرد نهایی و الزامات محیطزیستی و ایمنی، اهمیت زیادی دارد:
- استابلایزرهای پایه کلسیم-زینک (Ca-Zn): این ترکیبات به عنوان جایگزینهای بدون سرب معرفی شدهاند و به دلیل غیرسمی بودن، در کاربردهای حساس نظیر صنایع غذایی، پزشکی و اسباببازیها استفاده میشوند. آنها عملکرد پایدار و سازگار با استانداردهای زیستمحیطی دارند.
- استابلایزرهای پایه باریم-زینک (Ba-Zn): مناسب برای فرآیندهای اکستروژن، کلندرینگ و تولید فیلمهای PVC هستند. این ترکیبات قابلیت ایجاد شفافیت بالا، پایداری نوری و حرارتی مناسب را دارا میباشند.
- استابلایزرهای پایه قلع (Tin): عمدتاً در تولید محصولات شفاف استفاده میشوند. قلع با قابلیت تثبیت حرارتی و نوری بالا، انتخابی ایدهآل برای تولید بطریها، فیلمهای بستهبندی و کاربردهای پزشکی محسوب میشود.
- استابلایزرهای پایه سرب (Pb): علیرغم عملکرد بالای این ترکیبات از نظر حرارتی و مکانیکی، به دلیل خطرات زیستمحیطی و محدودیتهای قانونی در بسیاری از کشورها، کاربرد آنها به شدت کاهش یافته است.
- استابلایزرهای ترکیبی با پایه Ba-Cd-Zn: ترکیبات کادمیوم، گرچه در گذشته به عنوان یک پایدارکننده مؤثر مورد استفاده قرار میگرفتند، به دلیل سمیت بالا، امروزه تقریباً حذف شدهاند.
کاربردهای صنعتی استابلایزر حرارتی
استابلایزرهای حرارتی در انواع فرمولاسیونهای PVC بهکار میروند و دامنهی کاربرد آنها بسیار وسیع است. برخی از رایجترین موارد استفاده عبارتاند از:
- پروفیلهای در و پنجره (UPVC)
- لوله و اتصالات ساختمانی و صنعتی
- ورقهای کلندر و فومیزه
- کفپوشهای سخت و نرم
- چرم مصنوعی
- فیلمهای شرینک، استرچ و کلینگ
- کاغذ دیواری و پوششهای تزئینی
- ژئوممبرانها و محصولات ژئوتکنیکی
- شلنگهای صنعتی و خانگی
- سیم و کابل برق
- تجهیزات پزشکی حاصل از اکستروژن یا تزریق
اهمیت استابلایزر حرارتی در فرمولاسیونهای بازیافتی
در سالهای اخیر، بازیافت مواد PVC به دلیل مزایای زیستمحیطی و اقتصادی مورد توجه قرار گرفته است. اما مواد بازیافتی به دلیل پیشزمینه تخریب و استفاده مجدد، حساسیت بیشتری به گرما و فرآیند دارند. افزودن این استابلایزر در فرمولاسیون این دسته از مواد، موجب حفظ کیفیت، افزایش پایداری و امکان استفاده مجدد مؤثر از پلیمرهای مستعمل میشود.
مزایای کلیدی استفاده از استابلایزر حرارتی در PVC
استفاده بهینه از این استابلایزر در فرمولاسیون PVC مزایای زیر را به همراه دارد:
- افزایش مقاومت حرارتی پلیمر در طی فرآیند
- کاهش زردی و تغییر رنگ در محصول نهایی
- بهبود فرآیندپذیری و روانکاری در حین تولید
- ارتقاء خواص سطحی، نوری و مکانیکی محصول
- کاهش دود و بازدارندگی شعله در محصولات خاص
- افزایش راندمان تولید و کاهش ضایعات
- حفظ ثبات ابعادی و زیبایی ظاهری محصول
نتیجهگیری
این استابلایزر یک جزء کلیدی در ترکیب فرمولاسیون PVC محسوب میشود که در صورت انتخاب درست و استفاده مهندسیشده، نهتنها کیفیت و دوام محصول را تضمین میکند، بلکه پاسخگوی الزامات زیستمحیطی و فنی در کاربردهای متنوع خواهد بود. شرکت پلیمر پیشرفته دانا با عرضه انواع گریدهای پیشرفته این استابلایزر از برندهای معتبر جهانی، نقش مهمی در تأمین نیاز صنایع مختلف در داخل کشور ایفا میکند. انتخاب صحیح نوع استابلایزر، درصد مصرف و تطابق آن با شرایط فرآیندی و نیاز نهایی، کلید موفقیت در تولید محصولات باکیفیت، ایمن و پایدار از جنس PVC است.